在全球化競爭日益激烈的今天,企業若想在市場中脫穎而出,必須不斷提升生產效率,降低成本,並提高產品品質。精實管理是通過消除浪費來實現持續改進的管理哲學,核心觀念是投入最少資源創造最大價值,運用精實管理改善生產作業流程,能有效地消除生產過程中的浪費,達到提升效率、降低庫存、縮短交期等目的。
.精實管理的基本理念:
精實的概念源自豐田生產系統(TPS,Toyota Production Sys-tem),精實管理一詞是由麻省理工學院的教授及專家所創,因在他們研究及調查中發現日本豐田汽車的生產方式,最適用於現代製造業。以下介紹其核心理念,包括TPS的2大主軸以及精實管理的5大原則與要避免的8大浪費。
.TPS 的2大主軸
TPS最重要的兩大主軸就是「即時生產」(Just in Time, JIT)與「自働化」。所謂JIT 就是在必要的時間,到必要的地方,拿取必要數量的必要物品,消除製造現場不必要的浪費,提升生產效能。自働化則是當問題發生時,機器會自動停止,將問題顯現出來,並且馬上找出原因解決問題,防止相同問題再次發生,此方式把人的智慧賦予機械上,因此在自動化的動加上人字旁,稱為自働化。
.精實管理的5大原則
1.確定價值(Value):從顧客的角度確認產品(或服務)的價值所在,哪些活動是真正創造價值。
2.掌握價值流程(Value Stream):確認產品的設計、銷售、製造等各項措施,進一步消除浪費所在,掌握價值流程。
3.暢流無阻(Flow):重新思考工作方法和選擇適切工具,讓產品各生產環節皆能像溪流般以連續暢流的方式進行,力求價值活動暢通無阻。
4.拉式管理(Pull):在客戶有需求時,給他們所想要的產品或服務,建立由顧客需求驅動生產的「拉式管理」。
5.追求完善(Perfection):從小規模的改善開始,藉由有效率地追求突破及漸進式努力,追求無止盡的完善。
.精實管理要避免的8大浪費
1.生產過多的浪費:製造比客戶或下游工程所要求的量多、速度快或是交期早。生產過多的浪費為最根本之浪費,容易造成其他大部分之浪費。
2.等待的浪費:作業者什麼也沒做、等待的狀態。例如等待機械作業完了或設備的修復,或是等待零件的延遲送達。
3.搬運的浪費:搬運本身就是浪費,因為搬運沒有產生附加價值。零件或製品是有必要搬運,但搬運的浪費要越小越好。
4.加工的浪費:不必要的加工、不正確的加工。
5.庫存的浪費:擁有多餘的庫存(原始材料、半成品、完成品)。
6.動作的浪費:作業者/機械的動作中,沒有產生附加價值的動作。
7.不良品的浪費:製造出不良品,導致產品須被檢查、重工、報廢。
8.未被使用的員工創造力:未使員工參與投入或未能傾聽員工意見,造成未能善用員工的時間、技能與構想,使員工失去改善與學習的機會。
透過掌握以上精實管理的基本理念,搭配對應的精實管理工具與活動,例如:5S運動(整理、整頓、清掃、清潔、素養)、可視化、標準化、看板管理、平準化生產、快速換模、全面生產管理、全面品質管理、品管圈、團隊合作等,即可達成消除浪費提高生產效率,並以最少資源創造最大價值。過程中若有專業的顧問帶領與公司全員的參與,可達到事半功倍的效果,而政府資源的投入更可協助產業的推動。
.產業發展署協助業者導入精實管理
產業發展署積極協助企業推動精實管理,自109年起委託機械公會辦理TPS精實管理補助計畫,迄今已促成百案以上的廠商投入精實生產,推動產業涵蓋機械、機械零組件、精密模具與車輛零組件、紡織等,以下介紹幾個案例。
.榮富工業打造一台流生產模式 大幅提升營收及生產效率
榮富工業是國內複合式鑽銑床及金屬帶鋸床專業製造商,總經理林奕杰看到台灣引興公司推行TPS達極致,幾乎零庫存,創造出高效率生產,因此透過產業發展署TPS補助計畫導入精實管理,先去除浪費,做好製程標準化,透過數位化收集製程參數數據,並以切高麗菜為例,創造了獨特的「一台流」數位精實生產模式。
榮富工業導入精實管理後,提升機台組裝作業生產作業效率約29%(每台從140分鐘減至100分鐘),此外透過公司上下的齊心努力,員工漸漸地感受到改革帶來的轉變,營收成長3成。後續更以自身的導入經驗,推廣至供應鏈體系,以帶動整體產業的升級轉型。
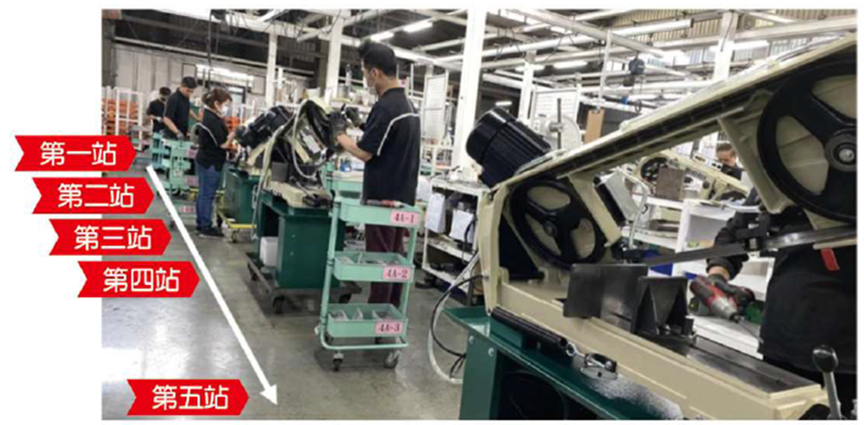
圖:榮富工業應用精實管理,建立分站拉式生產線
.鉅祥企業結合數位化與TPS 優化生產製造流程提升競爭力
鉅祥企業專精於精密連續沖模設計製造,為高品質車用、醫療與3C電子零組件的生產廠商,應用產業發展署補助計畫資源,將車用零件生產線,導入精實管理生產,以強化製程鏈結能力、精進換模流程、店面管理資訊可視化等3大主軸逐步推動,成功優化生產製造流程,藉由即時串聯物料及產線資訊,建立可視化資訊看板,也透過分析廠內製程,精進模具更換流程,並可依照客戶需求,即時管理店面及庫存物料,減少因庫存產生的相關費用。
鉅祥企業導入精實管理後,降低換模時間36%,降低包裝材料半成品庫存64%、縮短前置時間30%,解決傳統批量生產造成大量庫存的瓶頸,營收成長34%,成功提升公司競爭力。此計畫的推動不但讓鉅祥企業成功優化整體製造流程,公司也透過獎勵方式不斷的優化建立精實文化。
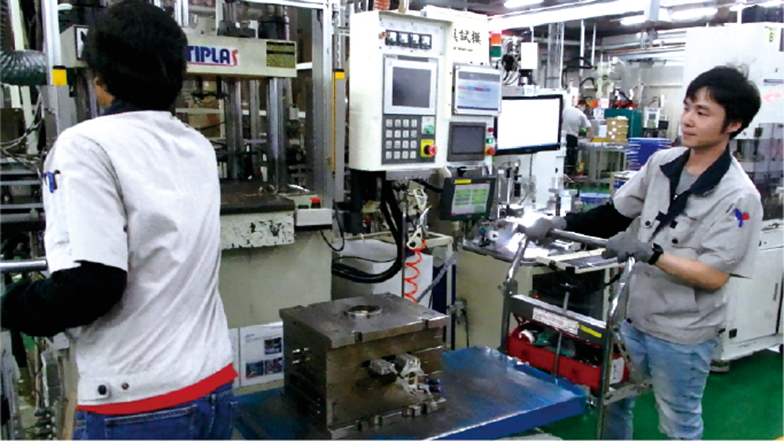
圖:鉅祥企業導入精實管理,降低加工換模作業時間
企業的轉型,除了有形的軟硬體投資,在升級的過程中,也要經由經營者與全體員工的心態改變,來重塑企業文化以提升管理與生產效率;而要重塑無形的企業文化,TPS精實管理便是最好的手段;在淨零碳排的國際趨勢下,藉由精實管理的消除浪費與提升能效,將有助於廠商跟上時代浪潮。